Visakhapatnam: Recurring accidents in industrial areas raise many questions
The recent gas leak incident at LG Polymers claimed 12 lives and hospitalised over 500 in Visakhapatnam
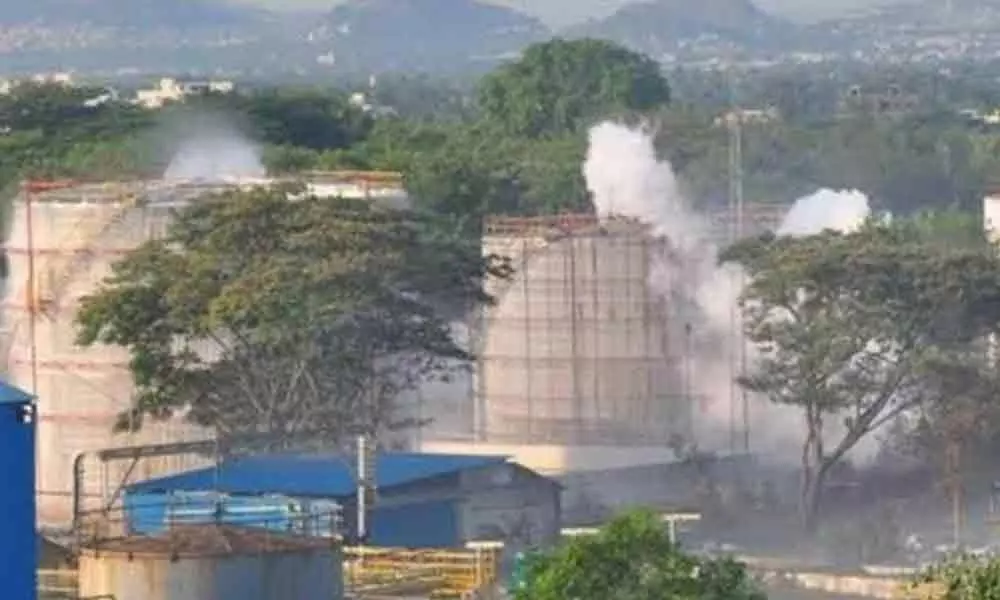
Visakhapatnam: Three industrial accidents in a row in which 15 persons lost their lives rocked the City of Destiny putting a question mark on the safety of people.
In May, there was a styrene monomer leak at LG polymers followed by a similar incident at Sainor Life Sciences Private Limited on June 29. Two weeks later, an inferno engulfed the solvent recovery facility Visakha Solvents.
For the last eight years, over 40 had lost their lives in about 30 accidents that occurred at JNPC. This apart, oxygen pressure reduction station blast at Visakhapatnam Steel Plant and fire accident at HPCL Visakh Refinery were some of the major incidents that killed over 45 persons in the past.
Industrial mishaps continue to happen in Visakhapatnam which is considered an industrial hub of the State, raising public alarm at frequent intervals.
The High Power Committee (HPC) formed to investigate the gas leak incident at LG Polymers, pointed out that negligence and safety lapses happen to be the prime reasons that led to the mishap.
Not just the HPC, a slew of committees formed to investigate industrial accidents cite similar reasons.
When The Hans India team discussed with the experts and officials concerned about recurring industrial accidents, they say that inadequate training for the staff, lack of safety mechanism, poor adherence to safety norms, recruitment of unqualified staff to handle machinery and absence of required material to counter the gas emissions appear to be the main causes resulting in recurring mishaps.
Following a series of mishaps that happened in Visakhapatnam, the biggest question that arises is whether the district administration is focusing on preventing incidents from recurring. Six decades ago, the tank used to store molasses at LG Polymers was later utilised for styrene monomer storage. Such a glaring miss makes one wonder what kind of aspects were looked into while conducting a safety audit of the industries.
"On-site and off-site emergency plans should be readied in all the industries. They include, providing training to the staff in handling any emergency situation, awareness programmes on contingency plans among the locals and education on the direction of the wind wherein industries deal with hazardous chemicals will help people shift to safer zones in case of any emergency. Keeping the maximum risk involved in view, industries should come up with preventive steps. Most industrial accidents happen due to non-compliance with safety norms," opines Dwibhashyam Rajeswara Rao, former technical committee member of the Pollution Control Board.
Elaborating the proactive role of the management in accident prevention mechanism, District Fire Officer B V S Ram Prakash says, "The effort should be more on taking preventive measures to avert an accident in the first place. Though the no objection certificates (NOC) for fire safety to the industries are granted based on their adherence to the safety standards, fire control systems fail to work during emergencies if they are not maintained properly. This way, there is a larger scope for a minor mishap turning into a catastrophe."
Experts say that below 40 per cent of the industries follow safety standards and the rest continue to flout them. Committees that are formed post an industrial accident should not be confined to investigating into a mishap alone but look into a larger picture. The need of the hour is taking concrete steps to prevent industrial accidents from recurring along with ensuring industries' compliance with the safety norms, conducting regular inspection, making mock drills in handling emergency situations mandatory and, above all, taking stringent action against the erring industries.
As industrial accidents continue to claim the life of workers, the management of the companies should look beyond the formal reviews and make sure that they do not overlook a glaring miss.