Live
- Maoist Leader Manjula Surrenders in Warangal, Receives ₹20 Lakh Reward
- Kartika Purnima celebrations fervour marks Telugu States, devotees flock to shiva shrines
- YSRCP alleges meagre fund allocations for Super Six schemes
- Telangana CM Reviews Plans for First Anniversary of State Government
- Vijayawada: Kindness Day celebrated
- Rajamahendravaram: Students advised to set clear goals
- Digital locker facility now available at Namma Metro stations
- Swarna Vaijayanthi Mala presented to Tirumala god
- Physical fitness mandatory for cops: SP Jagadeesh
- Children’s Day celebrated at Ananthalakshmi School
Just In
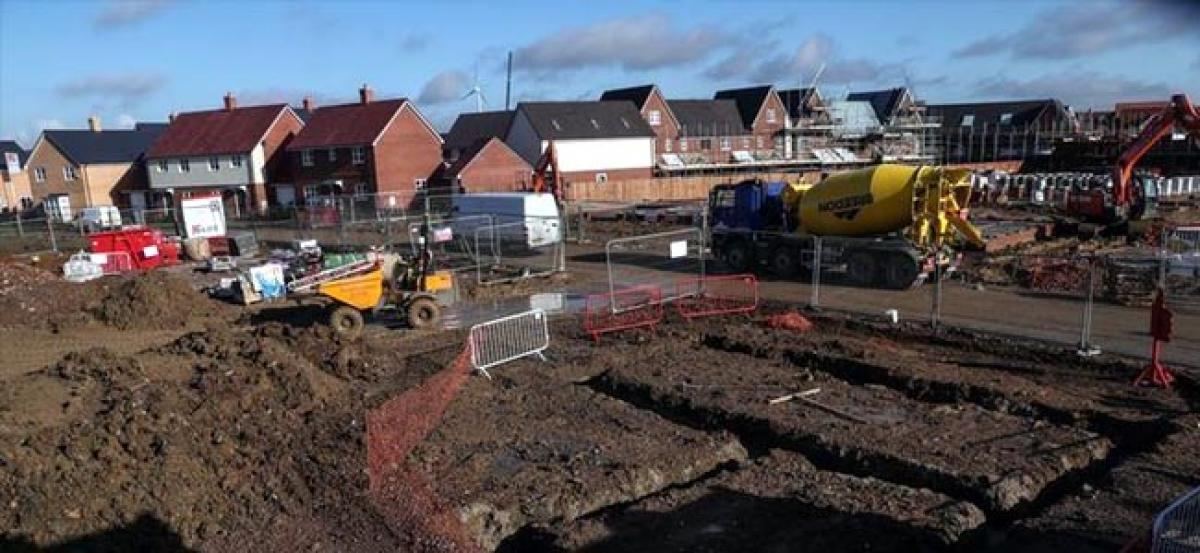
The prospect of Brexit choking off the supply of EU workers is reshaping Britain\'s homebuilding industry, with big companies increasingly looking to factory-manufacture houses in sections that can be slotted together on-site with minimal labour.
The prospect of Brexit choking off the supply of EU workers is reshaping Britain's homebuilding industry, with big companies increasingly looking to factory-manufacture houses in sections that can be slotted together on-site with minimal labour.
Many of Britain's leading housebuilders, including Berkeley, Taylor Wimpey, Persimmon and Your Housing, told Reuters they were either planning new developments of prefabricated homes or considering doing so.
This represents something of a turnaround in a country where "prefabs" have borne a strong and lingering stigma dating back to the 1940s when Winston Churchill ordered tens of thousands of cheap, flimsy, ugly units to be built to address a shortage housing after World War Two.
The change is being fuelled by fears over a labour shortage in the British construction industry, which relies heavily on European workers like carpenters, joiners and bricklayers. About 12 percent of its 2.1 million employees come from abroad, mainly the EU, according to official figures. The trend is amplified in London where a quarter of the 350,000 construction employees come from other EU countries, particularly eastern Europe.
Britain leaving the European Union, with its single market and free movement of workers, threatens the flow of this crucial skilled labour at a time when the country faces another housing shortage and is looking to build 1 million homes by 2020.
This is driving a resurgence in so-called offsite construction which allows anything from bathroom pods and chimneys to entire houses to be manufactured in factories before being transported by trucks to the site and bolted together.
While this involves a bigger initial investment, it requires a fraction of the labour of traditional construction, which relies on armies of workers to build houses layer by layer from the ground up. The imperative to avoid delays from labour shortages can dramatically push up payroll costs.
"Fundamentally, the construction industry has been doing some things the same way for hundreds of years. Historically, we had the labour ... But the challenge is different now," said Berkeley Chairman Tony Pidgley.
BIG PLAYERS
Berkeley is producing its first ever factory-built homes this year. It is starting small, with 16 prefabs in southeast London, but has another 50 in the pipeline for the capital and plans to gradually expand the programme.
The company said it had a target of building 10-15 percent of all its houses using modular construction in the "short to medium term", without giving a more specific timeframe. It added that factory work could be carried out by fewer, and relatively unskilled, workers as most processes were automated.
Your Housing, which has a greater focus on social housing, is taking a different approach and partnering with Chinese companies to undertake a far bigger project.
It said it was finalising an agreement with China National Building Material (3323.HK) and WeLink for a 2.5 billion pound joint venture to build six prefab factories in Britain, one a year to 2022, with the aim of producing thousands of homes.
Your Housing executive director Stephen Haigh said Britain's EU withdrawal would challenge traditional building by squeezing labour, allowing factory-based construction to flourish.
Mark Farmer, author of a government-commissioned review into the construction sector labour market late last year, said the Brexit vote was forcing companies to look at offsite building techniques, to reduce dependence on traditional labour.
"I'm not talking about a few thousand units, I'm talking about investors and developers that control the development of tens of thousands of units," Farmer, who runs the Cast real estate and construction consultancy, told Reuters.
PREFAB TECH
Britain lags other nations in the adoption of factory-based construction, which accounted for 7 percent of UK housebuilding by value in 2015 versus up to 15 percent in Germany and Japan, according to data from engineering consultancy Arcadis.
Today's technology is light years ahead of the low-grade 1940s prefabs, however, and prefabrication can produce homes of the same quality as traditional building techniques, drawing the interest of big construction players ahead of Brexit.
Taylor Wimpey is exploring ways to "future proof" its business and considering offsite construction options ranging from modular house sections to prefab timber frames, said divisional managing director John Gainham.
"Mindful of skill shortages, which is a big issue within the industry, and the implications of Brexit potentially, we've started to look at all the mainstream alternatives," he said.
Its rival Persimmon has for many years had a factory in central England, part of a business called Space4, that makes prefab timber frames for about 40 percent of all its houses.
Space4 is looking at proposals to either increase volumes at the existing factory or build another factory elsewhere in Britain, said Persimmon Homes Midlands chief Richard Oldroyd, adding this was being driven by a desire to reduce reliance on traditional labour like bricklayers, partly in light of Brexit.
It is also testing the construction of factory-based attic, or loft, rooms as well as various finishes for houses to further shift construction offsite, he added.
'FEEL THE FEAR'
A study carried out by the Steel Construction Institute consultancy estimated that prefabrication could reduce traditional on-site labour by 75 percent. Many of these workers come from Poland.
Your Housing's Haigh estimates its factories would require a tenth of the workforce required on a traditional project. Berkeley says prefabs will cut on-site production time from about 40 to 10 weeks for a typical house.
Such savings could prove important after Brexit, which Arcadis estimates could lead to Britain missing out on 215,000 traditional construction workers coming to the country by 2020, on top of any departures of existing workers.
The quality of prefab homes today is equal to those built using traditional techniques. But the big upfront investment to set up factories means they currently cost significantly more, with builders taking the hit as they must still offer homebuyers competitive prices. In years to come, and as the method gains popularity, the production costs are expected to fall sharply.
Insurer Legal & General (LGEN.L) - a big investor in real estate - spent about 55 million pounds last year to set up a prefabs factory in northern England.
Only the big names in construction can afford offsite at the moment because of the initial investment required, said Justin Gates of real estate consultant Knight Frank.
"Eventually, modular businesses will get better and be available for the small and medium-sized housebuilders to use, but I think, at the moment, it is probably beyond their reach."
Supplier Kingspan (KSP.I) provides a wide assortment of construction components and services to builders of all types, making it a barometer of shifts in industry techniques.
It said it had seen housebuilders demand more and more offsite products since last June's Brexit vote.
Companies focused on traditional construction were now asking for offsite supplies, while those already partly building offsite were pushing for more, said Mark Stevenson, managing director of Kingspan's timber solutions business.
"We're being pulled in a direction that customers want us to go in, from more work from the building site into the factory," he added.
"You can almost feel the fear among the contractors and housebuilders where they've been surviving on labour from outside the country."

© 2024 Hyderabad Media House Limited/The Hans India. All rights reserved. Powered by hocalwire.com